Inspirating Tips About Does Star Or Delta Draw More Current
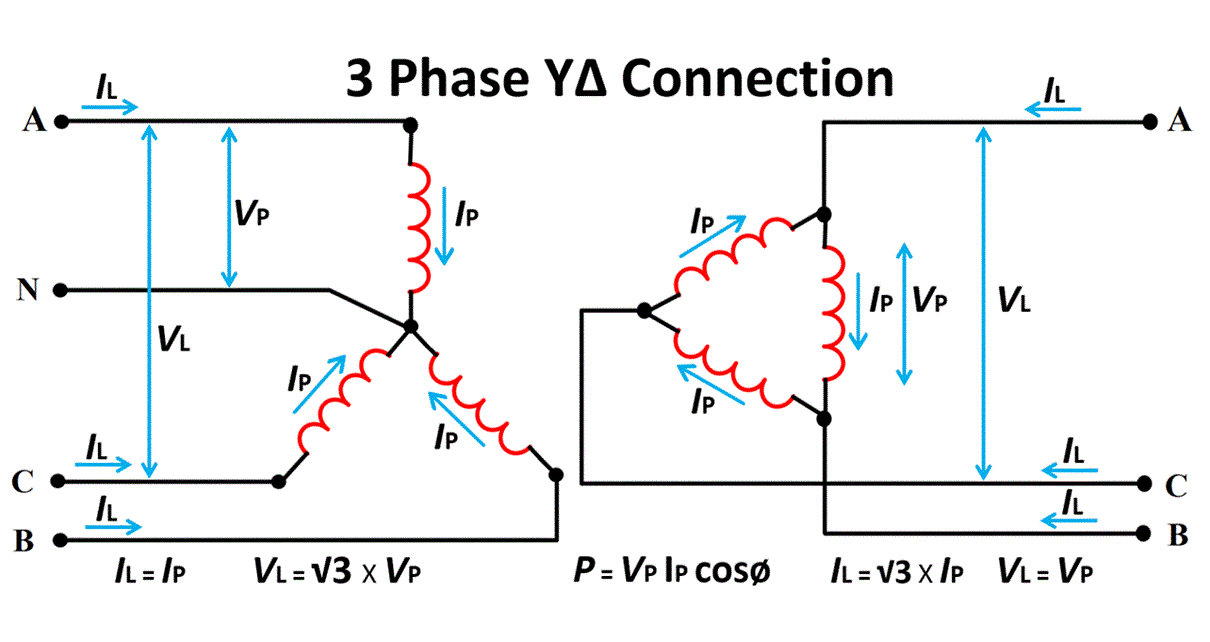
Star vs. Delta
1. Unveiling the Electrical Enigma
Ever wondered what's happening behind the scenes when you flip on a light switch or your AC kicks into gear? A big part of it involves electrical configurations called star (or wye) and delta connections. These aren't constellations or Greek letters just for show; they're crucial for how three-phase electrical systems deliver power. And one persistent question pops up: Does a star connection or a delta connection draw more current? Let's unravel this electrical enigma, shall we?
Imagine star and delta connections as two different ways to organize a team for a tug-of-war. In a star connection (also known as wye), three coils are connected to a central, neutral point, forming a "Y" shape. Think of it as everyone pulling from a common anchor. Delta, on the other hand, connects the coils in a closed loop, like a triangle, with no neutral point. Everyone's pulling against each other in a balanced way.
So, which team strains harder (draws more current) for the same amount of work (power delivered)? Well, the answer isn't a simple one-liner. It depends on a few things, mostly the voltage applied to each configuration and the load (the 'work' that the electricity needs to do, like powering a motor or a factory full of lights) connected to them. We're getting to the juicy details soon, promise!
This isn't about picking a winner, though. Understanding how these configurations behave is about selecting the right tool for the job. Choosing the wrong connection can lead to inefficiency, overheating, and even equipment failure. Trust me, nobody wants that kind of fireworks display (unless it's planned and safe, of course!). So, let's dive deeper and equip ourselves with the knowledge to make the right call.

Challenge Circuit 8 Infinispark
Current Draw
2. Delving into the Details
Alright, let's get a little more technical (but not too much, I promise!). The amount of current drawn by either a star or delta connection is intimately linked to the voltage applied and the load connected to it. The key is understanding the relationship between line voltage, phase voltage, line current, and phase current in each configuration. These are the variables that determine who's pulling harder in our electrical tug-of-war.
In a star connection, the line voltage (the voltage between any two of the three lines coming into the connection) is equal to 3 (approximately 1.732) times the phase voltage (the voltage across each individual coil). However, the line current is equal to the phase current. In simpler terms, you get a higher voltage but the same current on the lines as you do through each coil. It's like having a longer lever, you can move a heavier object with the same amount of force.
Delta connections flip the script. Here, the line voltage is equal to the phase voltage. However, the line current is equal to 3 times the phase current. So, the voltage is the same on the lines as through each coil, but the current on the lines is higher. Think of it as having more people pulling on the rope, the force on the rope increase.
Therefore, for the same load and power requirement, a delta connection will generally draw more line current than a star connection. But it's crucial to remember this is only if the voltage levels are designed to operate correctly with their respective connections. Simply connecting the same load to a star and then a delta setup (without adjusting voltage levels) will lead to very different results, potentially damaging results!

Power Factor and Efficiency
3. The Bigger Picture
Current draw isn't the only thing to consider when choosing between star and delta connections. Power factor and efficiency also play crucial roles in determining the overall performance of the system. Power factor is a measure of how effectively electrical power is being used. A low power factor means you're not getting the most bang for your buck; some of the power is being wasted. It's like spinning your wheels in mud.
Delta connections often have a better power factor than star connections, especially when dealing with inductive loads like motors. This is because the circulating current in the delta configuration can help to compensate for the reactive power drawn by the inductive load, improving the power factor. Improved power factor translates to lower energy bills and reduced strain on the electrical grid. Everybody wins!
Efficiency, on the other hand, refers to how much of the electrical energy you put in actually gets converted into useful work. No system is 100% efficient; some energy is always lost as heat. The type of load, the quality of the equipment, and the operating conditions all affect efficiency. While the connection type does contribute, it's often less significant than other factors.
Choosing between star and delta isn't just about which one draws more current; it's about optimizing the entire system for power factor, efficiency, and overall performance. It's about understanding the trade-offs and making the best choice for your specific application. Consider the specific motor or load that will be connected. Some motors are specifically designed for either star or delta start-up, which significantly changes the current draw at different stages of operation.

What Difference Between Star And Delta Connection Wiring Work
Applications
4. Putting Knowledge to Use
So, where do star and delta connections typically shine? Star connections are often used for power distribution because they provide a neutral point, which is essential for single-phase loads. They are also great for long distance transmission lines.
Delta connections, with their higher starting torque, are often used for starting large induction motors. A common technique is "star-delta starting," where the motor starts in a star configuration (lower starting current) and then switches to delta (higher running torque) once it reaches a certain speed. This reduces the stress on the power grid during startup.
Another application of delta connections is in transformers, especially those used in high-voltage transmission. The closed delta winding can help to suppress harmonics and improve the quality of the power supply.
Ultimately, the choice between star and delta depends on the specific application and the desired characteristics of the electrical system. There's no one-size-fits-all answer, but with a good understanding of the principles involved, you can make an informed decision. In short, it boils down to the load, the required starting current (if applicable), and the voltage levels being used.
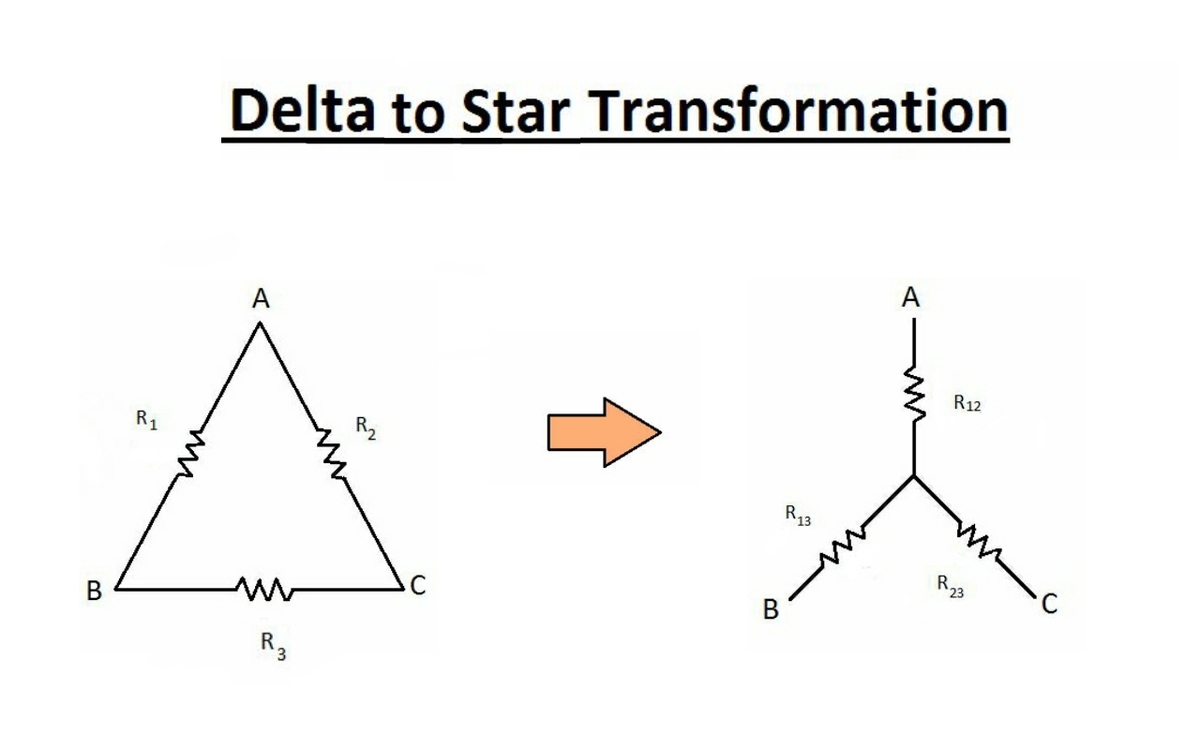
Transformasi Rangkaian Delta Ke Star Amateu Vrogue.co
Real-World Example
5. Practical Application in Action
Let's bring this home with a real-world example: the star-delta motor starter. Large induction motors can draw a huge amount of current when they start up, sometimes several times their normal running current. This can cause voltage dips and disrupt other equipment connected to the same power supply. Star-delta starters are a clever way to mitigate this issue.
The motor starts in a star configuration. Because of the voltage relationship in a star connection, the voltage applied to each motor winding is reduced, resulting in a lower starting current. This reduces the initial inrush of current and minimizes the stress on the power grid. It's like easing into a heavy workout instead of jumping straight into it.
Once the motor reaches a certain speed, the starter switches to a delta configuration. This applies the full line voltage to each winding, allowing the motor to develop its full torque and operate at its rated speed and power. It's like shifting gears to get up to cruising speed.
Star-delta starters are a practical example of how the principles of star and delta connections can be applied to solve real-world engineering problems. It demonstrates that neither configuration is inherently "better" than the other; they each have their strengths and weaknesses, and the key is to use them appropriately. This illustrates perfectly how the choice between the two depends heavily on application.

FAQs
6. Clearing up the Confusion
Still have some questions swirling around? Let's tackle some frequently asked questions about star and delta connections.
7. Question 1
Answer: Not always! For the same power output and when properly designed for their respective voltage levels, a delta connection will draw more line current. However, the phase current in a delta connection might be lower than the phase current in a star connection depending on the overall system design. Key words here are same power and proper design.
8. Question 2
Answer: Star connections are generally preferred for long-distance power transmission. The neutral point allows for grounding, which helps to protect against faults and surges. The stepped-up voltage can be then stepped down using transformers when arrive the destination.
9. Question 3
Answer: Yes, but it's not as simple as just rewiring the connections. You need to ensure that the motor windings are rated for the correct voltage and current levels. If the voltage is wrong, you will likely damage the motor. Consult the motor's specifications and a qualified electrician before attempting any modifications. It's definitely not a DIY project for the faint of heart!